96 Lichfield Street
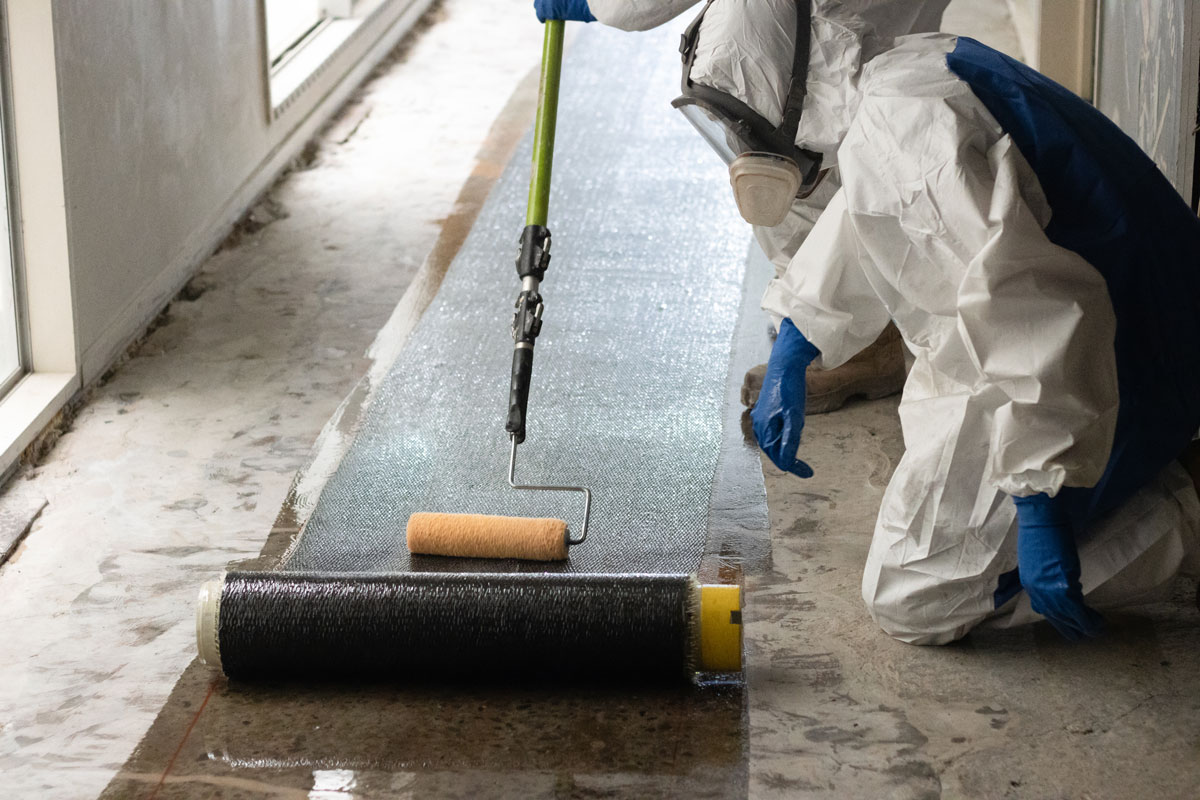
A category one heritage building, the challenge from the outset was to maintain the overall integrity of the historic facade, take care of the stone frontage, while giving the building strength and durability.
A category one heritage building, the challenge from the outset was to maintain the overall integrity of the historic façade, take care of the stone frontage, while giving the building strength and durability.
In 2020, The Connect Group was proudly selected as the strengthening and repair specialist for 96 Lichfield Street - better known to Christchurch locals as part of SOL Square (South of Lichfield).
First designed and built for Woollen Manufacturing company in 1919 by W. H. Gummer, the 110-room Living Space accommodation building had been vacant for almost 10 years, since the 2011 Christchurch Earthquake. A category one heritage building and the first of its kind to be constructed of reinforced concrete, we were tasked with completing structural strengthening and concrete repairs.
From the outset, the challenge was to maintain the overall integrity of the historic façade and take care of the stone frontage, all while improving the building’s strength and resilience against another seismic event. Steps such as securing the stone to the superstructure had to be undertaken to maintain the façade and stonework’s integrity.
The bulk of the repairs undertaken included concrete spalling repair to structural columns and beams throughout the building, followed by high-pressure epoxy injection repairs to shear load walls, columns, and floors. Supply, installation and construction of the new reinforcing steel, concrete sheer walls and basement transverse drag beams were also conducted.
We also opted for an alternative strengthening plan for the existing internal stairwell block walls, which were initially set for demolition. Instead, we applied an FRP (Fibre Reinforced Polymer) Strengthening System, making it more practical to reinforce rather than demolish. Additionally, in the basement, our team addressed water ingress issues by performing a polyurethane water stop injection to effectively seal the leaks.
Carbon Fibre Wrapping was a key strengthening component for this project due to its high strength capacity, lightweight and unintrusive nature. Carbon Fibre was applied to internal walls, structural columns, and floor diaphragms. This formed a major part of this project, with approximately 4600 metres being laid by The Connect Group during the project.
Working closely with the structural engineer’s plans, Carbon Fibre was applied to key walls and columns throughout the building in multiple ways, from the basement up to the fourth storey, to create a bracing element for key walls and columns. Some areas posed installation challenges, and this is where our vast experience came into play—collaborating with the project engineers to come up with alternative approaches to deliver the same design outcomes with less impact on the building overall.
The building continues to be one of Christchurch’s shining examples of a seismic-prone building being restored to its original glory for years to come.
At The Connect Group, we take pride in our early contractor involvement process, which enables us to collaborate with clients and engineering partners to develop practical, constructible solutions. This approach often results in substantial time and cost savings for our clients. Reach out to us today to discuss how we can help enhance the longevity of your building assets.